Armstrong At a Glance
Armstrong got its start in 1928 and earned a fast name as a trusted and reliable brand. They are committed to learning and innovating their HVAC solutions, and it’s an important part of their ethos that they produce durable units that provide comfort for homeowners. Each product goes through testing and tweaking to create a solution that their technicians would install in their home.
Other General A/C Maintenance Tips
1. Clean around your unit
2. Clean and straighten the fins
3. Level your unit
Get Quotes
How soon are you looking to buy?*
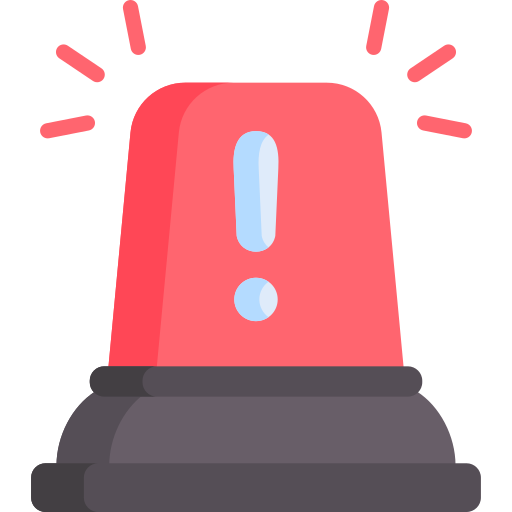
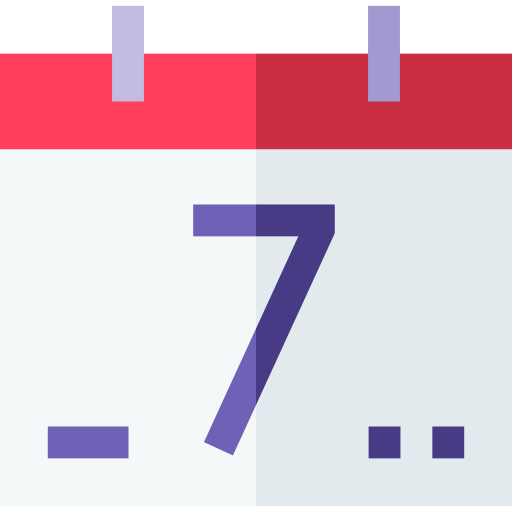
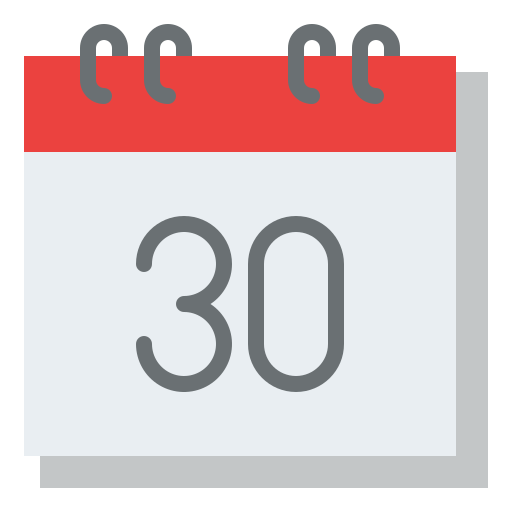
What’s Wrong With Your Armstrong Air Conditioner?
Armstrong Air Conditioner Error Codes
Error Codes
Alert Codes | Inverter Codes | Red LED Flash Code | Green LED Flash Code | Priority | Description |
---|---|---|---|---|---|
E345 | N/A | N/A | N/A | Critical | Heat Pump or Air Conditioner Alert Code - The "O" relay on the outdoor board has failed. Either the pilot relay contacts did not close, the relay coil did not energize or the circuit that confirms this operational sequence is not sensing properly. |
E409 | N/A | N/A | N/A | Moderate | Outdoor control secondary voltage is 18VAC or less. |
E410 | N/A | N/A | N/A | Moderate | The outdoor unit cycled off due to low pressure switch opening. |
E411 | N/A | N/A | N/A | Critical | The low pressure switch has opened 5 times within one hour. As a result, the outdoor unit is locked out. |
E412 | N/A | N/A | N/A | Moderate | The outdoor unit high pressure switch has opened |
E413 | N/A | N/A | N/A | Critical | The high pressure switch has opened 5 times within one hour. As a result, the outdoor unit is locked out. |
E416 | N/A | N/A | N/A | Moderate/Critical | The outdoor coil sensor has malfunctioned. As a result the outdoor unit control will not perform defrost. |
E422 | N/A | N/A | N/A | Moderate | Compressor top cap switch exceeding thermal limit. |
E423 | 40 | 4 Flashes | OFF | Moderate/Critical | The inverter has detected a circuit problem |
E424 | N/A | N/A | N/A | Moderate | The liquid line temperature sensor has malfunctioned |
E425 | N/A | N/A | N/A | Minor | Outdoor control has increased minimum compressor speed to allow for proper oil return due to low ambient temperature. NOTE - Minimum speed adjustments begin at 45°F and increase to 100% minimum at 17°F. |
E426 | N/A | N/A | N/A | Critical | Excessive inverter alarms |
E427 | 21 | 2 Flashes | 1 Flash | Moderate/Critical | The inverter has detected a DC peak fault condition. If condition (55A or higher) is detected, outdoor unit compressor and fan stop. Anti-short cycle is initiated. If peak current (55A or higher) occurs 10 times within an hour, system is locked out. Indicates high pressure, condenser fan failure, locked compressor rotor or overcharge. To clear, disconnect power to outdoor unit and restart. |
E428 | 22 | 2 Flashes | 2 Flashes | Moderate/Critical | The inverter has detected a high main input current condition. |
E429 | 23 | 2 Flashes | 3 Flashes | Moderate/Critical | On a call for compressor operation, if DC link power in inverter does not rise above 180 VDC for 2 and 3 ton models, 250 VDC for 4 and 5 ton models, within 30 seconds, the control will display a moderate code. If condition is detected, outdoor unit will stop (Compressor and fan). Antishort cycles is initiated. If condition occurs 10 times within a 60 minute rolling time period, system will lock out and display a critical code. |
E430 | 26 | 2 Flashes | 6 Flashes | Moderate/Critical | Compressor start failure |
E431 | 27 | 2 Flashes | 7 Flashes | Moderate/Critical | Error occurs when PFC detects an over-current condition of 100A, the control will display a moderate code. If condition is detected, outdoor unit will stop (Compressor and fan). Anti-short cycle is initiated. Inverter is unavailable to communicate with the outdoor control for 3 minutes. If condition occurs 10 times within a 60 minute rolling time period, system will lock out and display a critical cod |
E432 | 28 | 2 Flashes | 8 Flashe | Moderate/Critical | The inverter has detected a DC link high voltage condition. |
E433 | 29 | 2 Flashes | 9 Flashes | Moderate/Critical | The inverter has detected a compressor over-current condition |
E434 | 53 | 5 Flashes | 3 Flashes | Moderate/Critical | Outdoor control has lost communications with the inverter for greater than 3 minutes. Outdoor control will stop all compressor demands, recycle power to the inverter by de-energizing the contactor for 2 minutes. If this occurs 3 time in one thermostat call, the outdoor unit will locked out and display a critical code. |
E435 | 60 | 6 Flashes | OFF | Moderate/Critical | Inverter internal error. |
E436 | 62 | 6 Flashes | 2 Flashes | Moderate/Critical | Inverter heat sink temperature exceeded limit. Occurs when the heat sink temperature exceeds the inverter limit. Inverter issues code 13 first, then slows down to allow the heat sink to cool. If temperature remains high, outdoor unit stops (compressor and fan). Anti-short cycle is initiated. If condition occurs 5 times within an hour, system is locked out. To clear, disconnect power to outdoor unit and restart |
E437 | 65 | 6 Flashes | 5 Flashes | Moderate/Critical | Heat sink temperature sensor fault has occurred (temperature less than 4ºF or greater than 264ºF after 10 minutes of operation). |
E438 | 73 | 7 Flashes | 3 Flashes | Moderate/Critical | The inverter has detected a PFC over current condition. This would be caused by a high load condition, high pressure, or outdoor fan failure. Outdoor control will display the code when the inverter has the error. After 3 minutes, the inverter will reset and the compressor will turn on again. If it happens 10 times within a 60 minute rolling time period, the OD control will lock out operation of the outdoor unit and display a critical code. |
E439 | 12 | 1 Flash | 2 Flashes | Moderate | Compressor slowdown due to high input current. |
E440 | 13 | 1 Flash | 3 Flashes | Moderate | Heat sink temperature is approaching limit. The compressor speed automatically slows to reduce heat sink temperature. The control sets indoor CFM and outdoor RPM to values according to demand percentage rather than the actual Hz. Alarm is automatically cleared. |
E441 | 14 | 1 Flash | 4 Flashes | Moderate | Compressor slowdown due to high compressor current. Compressor current is approaching limit. The compressor speed automatically slows. The control sets indoor CFM and outdoor RPM to values according to demand percentage rather than the actual Hz. Alarm is automatically cleared. |
E442 | N/A | N/A | N/A | Critical | The top cap switch has opened five times within one hour. As a result, the outdoor unit is locked out |
E443 | N/A | N/A | N/A | Critical | Incorrect appliance unit size code selected |
E600 | N/A | N/A | N/A | Critical | Compressor has been cycled OFF on utility load shedding. |
E601 | N/A | N/A | N/A | Critical | Outdoor unit has been cycled OFF on low temperature protection |
ArmstrongAir Conditioner Repair Costs
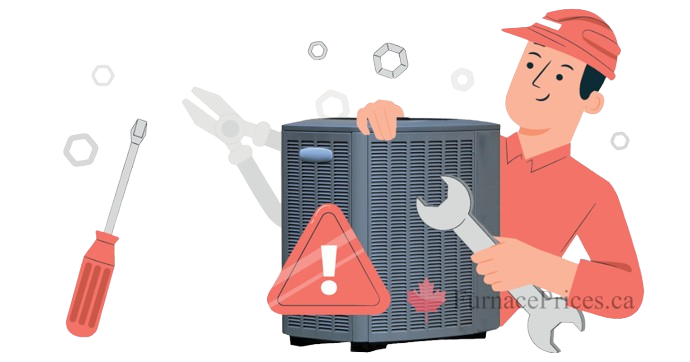